Autonomous Unmanned Vehicles Transform Bridge Inspections
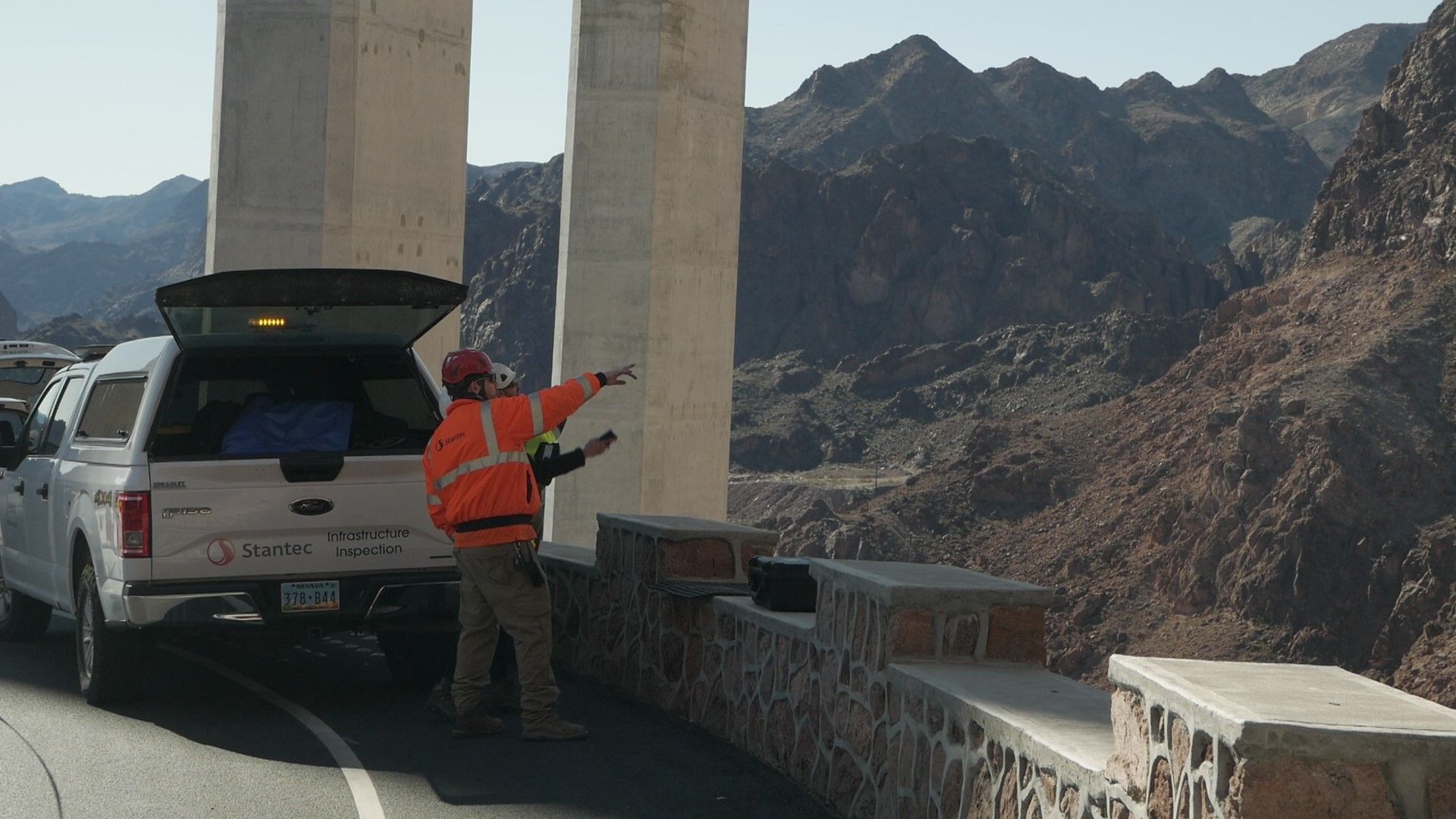
Keeping up with structurally deficient bridges is an ongoing challenge for virtually every bridge engineer and inspector in the U.S. Of the 620,588 bridges in the country, 42,951 — nearly 7% — were deemed structurally deficient last year, according to the Federal Highway Administration.
Aging infrastructure significantly contributes to the problem at hand. In 2022, half of the top 20 most frequently traveled bridges in the US were classified as structurally deficient, with an age of at least 60 years. The oldest among them dates back to 1932. According to a recent ARBTA report, 1 in 3 bridges need repair in the United States.
In 2021, the U.S. Department of Transportation estimated the total cost for repair or replacement of those structurally deficient bridges at over $54B. Many transportation departments face a potentially overwhelming avalanche of productivity and resource costs associated with large numbers of aging bridges.
That backlog of deferred maintenance can’t be accomplished all at once, so transportation departments need to prioritize while continuously monitoring the condition of all bridges in their jurisdiction.
Bridge inspection challenges and costs
While bridge inspections need to be completed thoroughly, and as quickly as possible, the current process is slow and costly. A typical inspection may require inspection engineers, bucket trucks and operators, and climbers with ropes. If lanes of traffic must be closed, traffic control personnel and a police presence are also required. And those are just costs transportation departments can foresee. There may also be other unforeseen risks and hassles such as security and other safety considerations.
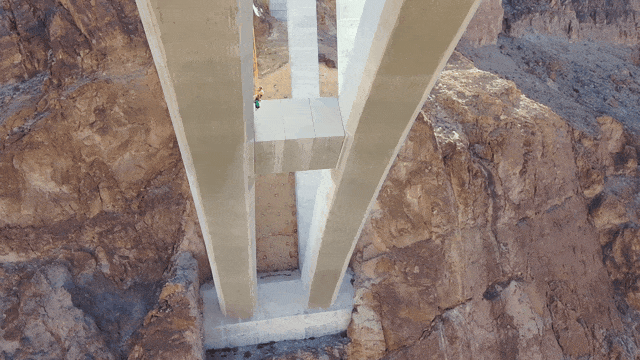
Federal Highway Administration requires that states inspect bridges following FHWA standards every two years, at a cost it estimates range from $4,500 to $10,000 per bridge, but some bridges can cost much more. And more frequent inspections may be required to track the condition of bridges with known defects.
Revolutionizing bridge inspections
In response, engineers at many DOT organizations have begun using uncrewed aerial systems (UAS) for bridge inspections. These remotely controlled drones save time and reduce costs by enabling faster —and safer — visual inspections of bridge structures. A UAS can reach areas of a bridge that are difficult to reach manually using bucket trucks or climbers on ropes, and they don’t block lanes of traffic while in use.
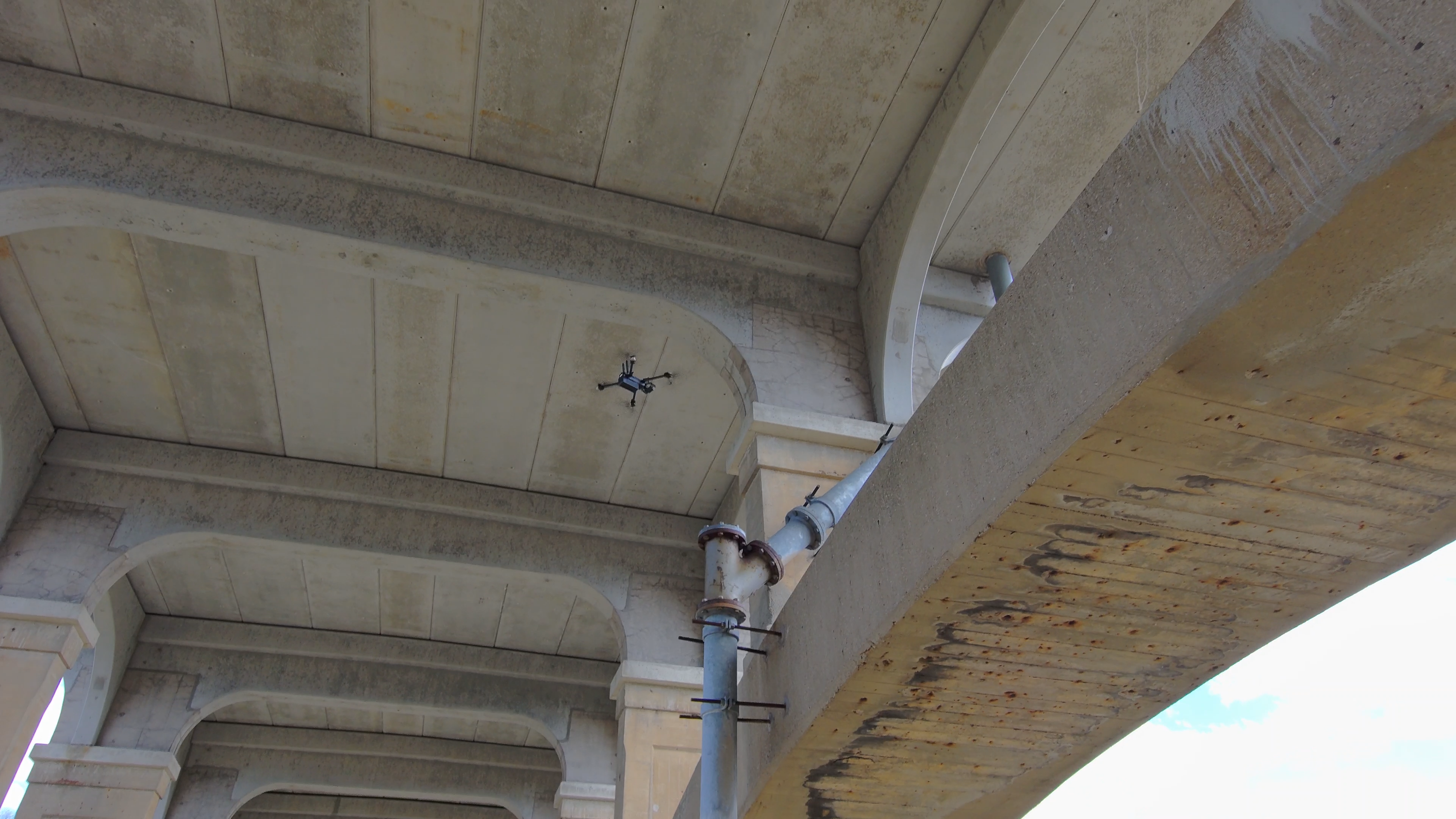
That’s why the use of UAS for bridge inspection is taking off. Market research firm Fact MR predicts that the market valuation for UAS in bridge inspections will grow at a compound average growth rate of 21.4% over the next decade.
"It's a real challenge to inspect bridges thoroughly under the time and labor constraints DOTs and subcontractors are up against,” said Alicia Llorens, principal solutions engineer at Skydio. “More and more organizations are equipping their engineers with drones as a tool to speed up and improve the quality of their inspections.”
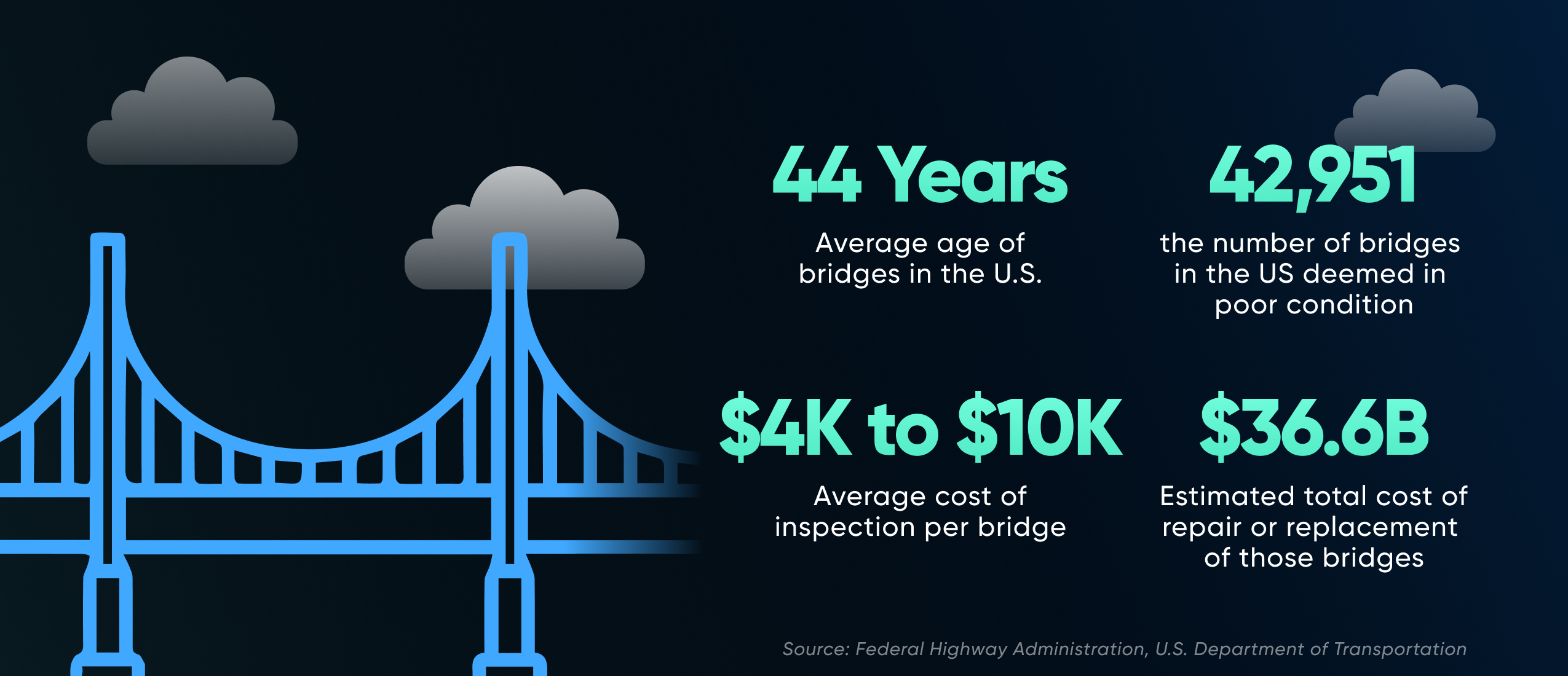
How UAS systems transform bridge inspection operations
“Currently, 28 state DOTs are using UAS technologies for bridge inspections — and that number is growing every day,” said Llorens at Skydio. A typical UAS system includes a drone equipped with a camera, navigation system and data link, and a ground control station and drone operator. Drone sizes vary: smaller units can get into tighter spaces but may have a shorter run time, while larger units may be able to stay in flight for longer periods and carry bigger payloads.
Unlocking Insights and Tracking Structural Changes:
With more advanced systems, image and video data that the UAS gathers can be uploaded into a photogrammetry system to generate a digital 3D model of the structure, called a “digital twin” (Photogrammetry is the processing of images to create a digital map of infrastructure in either 2D or 3D). Over time, engineers can add data from more recent inspections to the model to track changes to the structure over time. A typical flight time ranges from 20 to 35 minutes.
“Instead of having a hard copy of bridge anomalies that someone is to inspect, engineers can have a digital twin hosted in the cloud, and all of the stakeholders can see that information and analyze it,” said Llorens. An advanced drone system can create a “3D mesh” that can form the base layer for a CAD 3D mathematical model, she adds. “That CAD model can then be passed on to a civil engineer or architect.”
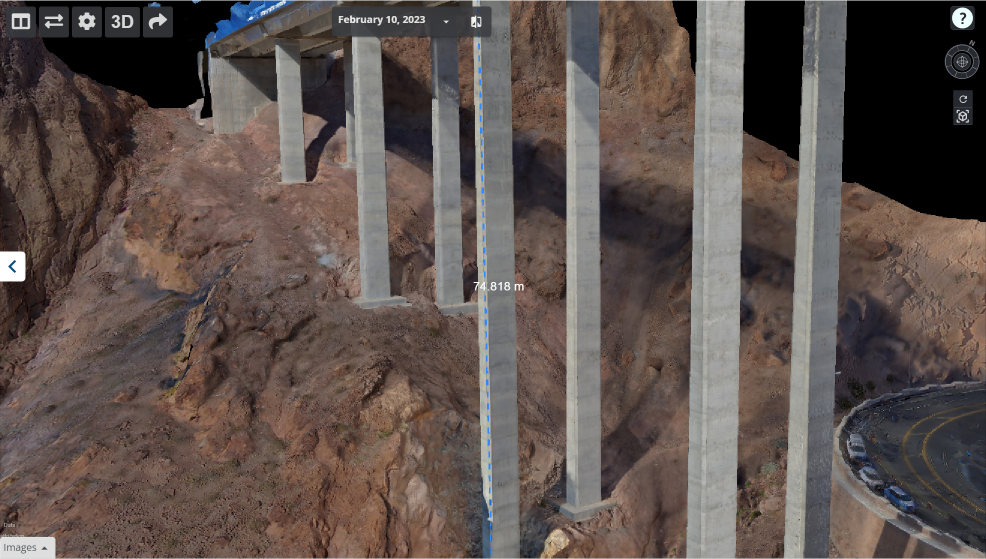
Limitations for traditional drones
Even for experienced pilots, avoiding collisions with bridge structures and other obstacles has been tricky — until recently. “We’ve been using drones since 2013,” said Michael Marshall, bridge engineer and senior associate at engineering and inspection firm Stantec in a webinar on the use of drones in bridge inspection. Early drones in the market at that time were manually controlled devices, such as the Intel Falcon 8, and the company subcontracted with licensed pilots to operate its drones. Having a dedicated pilot allowed engineers to focus on the bridge inspection, rather than worrying about obstacle avoidance. In addition, when drones flew into the underside of some structures they risked losing the GPS signal. Without navigational guidance drones could crash.
While manually operated, unassisted UAS helped with the inspection of bridge columns, they couldn’t get within arm’s length of structures or fly into tight spaces due to the risk of hitting the structure. “The GPS loss made us really uneasy,” Marshall said. “We were focusing more on the drone and not hitting the bridge than we were on gathering bridge inspection data.”
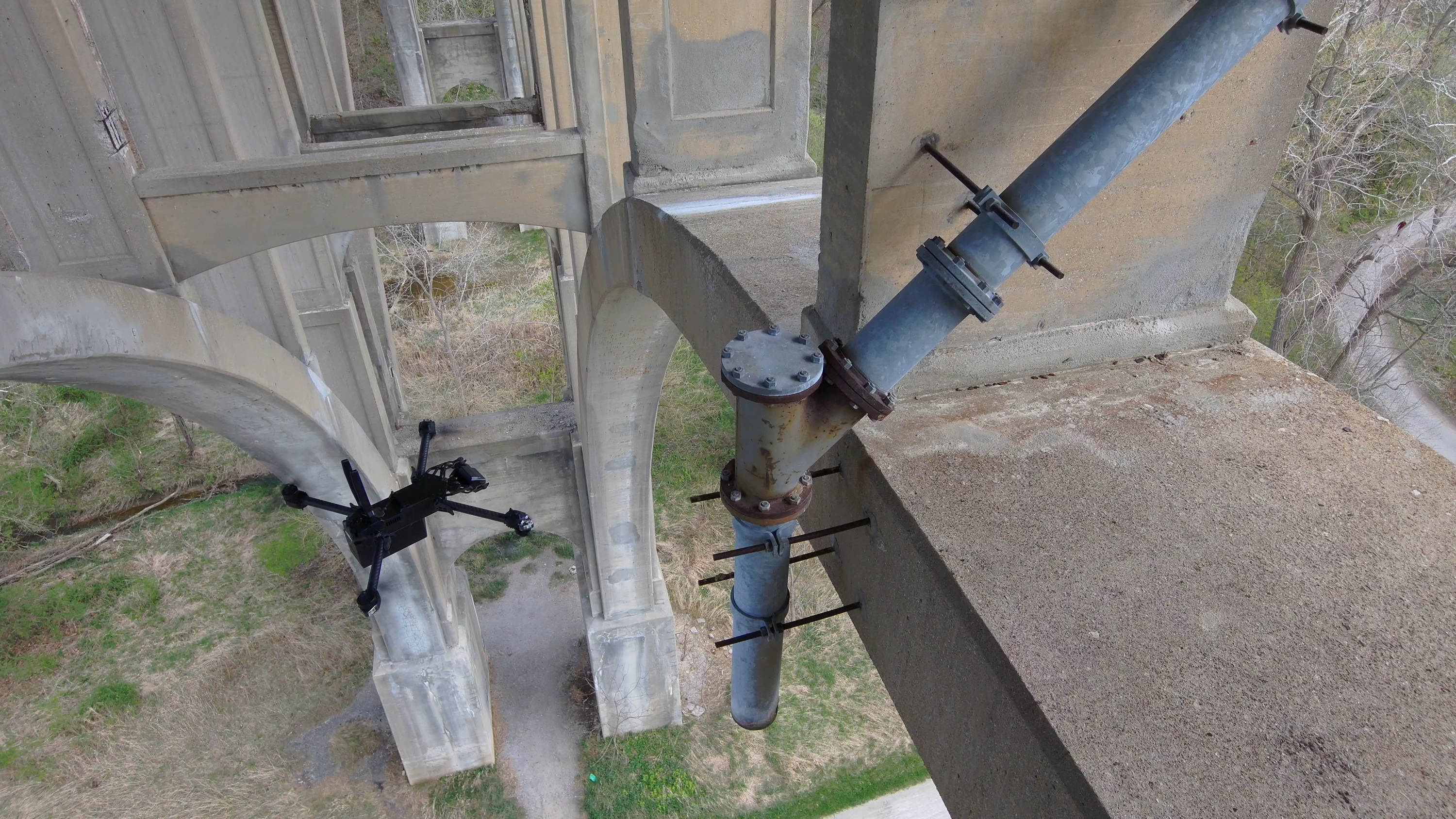
Next-generation UAS: Obstacle avoidance, visual navigation
Much has changed since then. For example, the Skydio UAS Stantec uses has obstacle avoidance and visual navigation technologies that cut down on training time and make piloting easy enough for engineers to operate the drones themselves. Skydio’s X2 can achieve closer visual inspections at higher resolution — it can be set to get as near as six inches from a structure - much closer than pilots of traditional drones might feel comfortable doing. This standoff distance matters because up close, engineers can see more detail. The tradeoff is that it takes longer to cover the whole bridge because you can’t see much of it at any given time.
To accomplish that, Skydio UAS drones include six navigation cameras controlled by a Nvidia super processor that includes built-in AI features. The system captures data continuously with a 360 degree view to provide awareness of its surroundings. Those features allow the system to function even in tight spaces under a bridge, where the guidance system’s GPS signal may be lost. “The drone can get into areas that the rope access and budget truck teams have difficulty accessing,”Marshall said. “These UAS take half the time, and require less than half the resources,” he said.
Efficiency Soars: Accelerating bridge inspection timelines and reducing costs
Before, a substantial bridge inspection project took two weeks with eight climbers, with four working on “snoopertrucks,” he adds. “Integrating drones brought that down to one week,” cutting costs from $211,000 to $105,000. Today, using the latest Skydio technology, that same project can be completed in about 2 ½ days with a drone team of three people,” he said. “You don’t have that fear of crashing into the bridge, and you can get up close to capture more data.”
And getting inspection engineers up to speed on the UAS is easier, said Llorens. “Traditional drones require a significant amount of training to operate, and once operators go on site, they need more training to be able to capture the data with specific requirements, such as data quality. That takes time, and it’s not scalable if you have to do that for all of your bridge inspectors. “Skydio automates the workflow of data capture so that anyone can leverage Skydio drones with minimal training,” Llorens said.
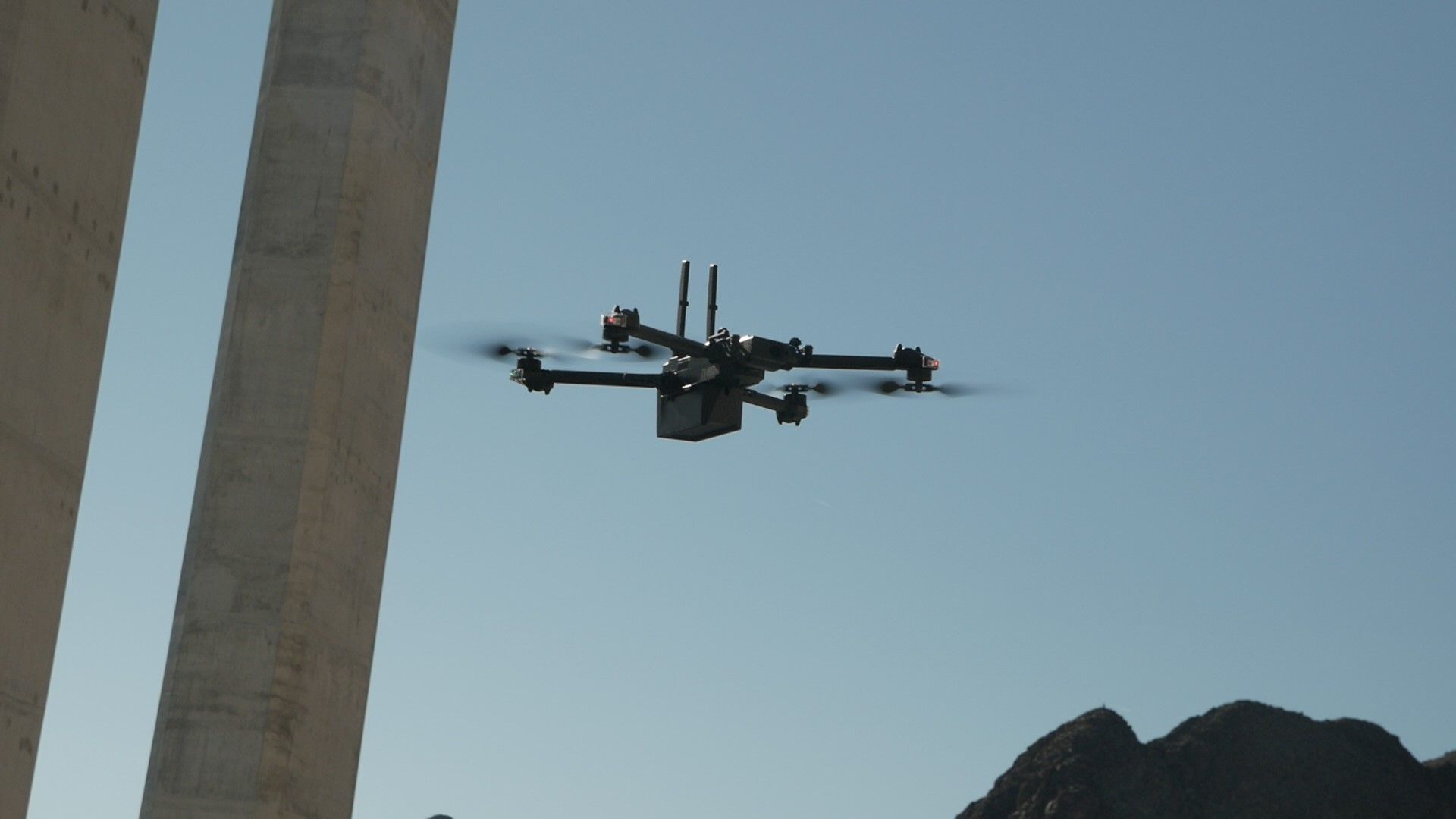
Better data, better decisions
Stantec’s bridge engineers don’t wait to get back to the office to review the data. “We review the 3D scans on site, and when we see something, we relay that back to the rope-access technicians who can rappel down to take a closer look,” said Marshall. “Hands-on access is still part of our industry, but the drones help us to hone in on specific locations.” You can also see if you have the video and image coverage needed to create the 3D model by viewing the raw, low-resolution images on the controller. That eliminates the need to have a drone go back a second time to fill in missing data you need to create a digital model, he adds.
Back in the office, the fully formed 3D models provide visual context that might be missing from the raw video and image data. On the ground, he said, “you’re at the mercy of how that video was captured and you can’t see what was around, say, staining on a pier,” said Marshall. Viewing it in the 3D model, however, might reveal that the source of staining was caused by a drain directly above it. “With a full 3D model you can see the causes, not just the defect, and you can see how they’re propagating from year to year,” he said.
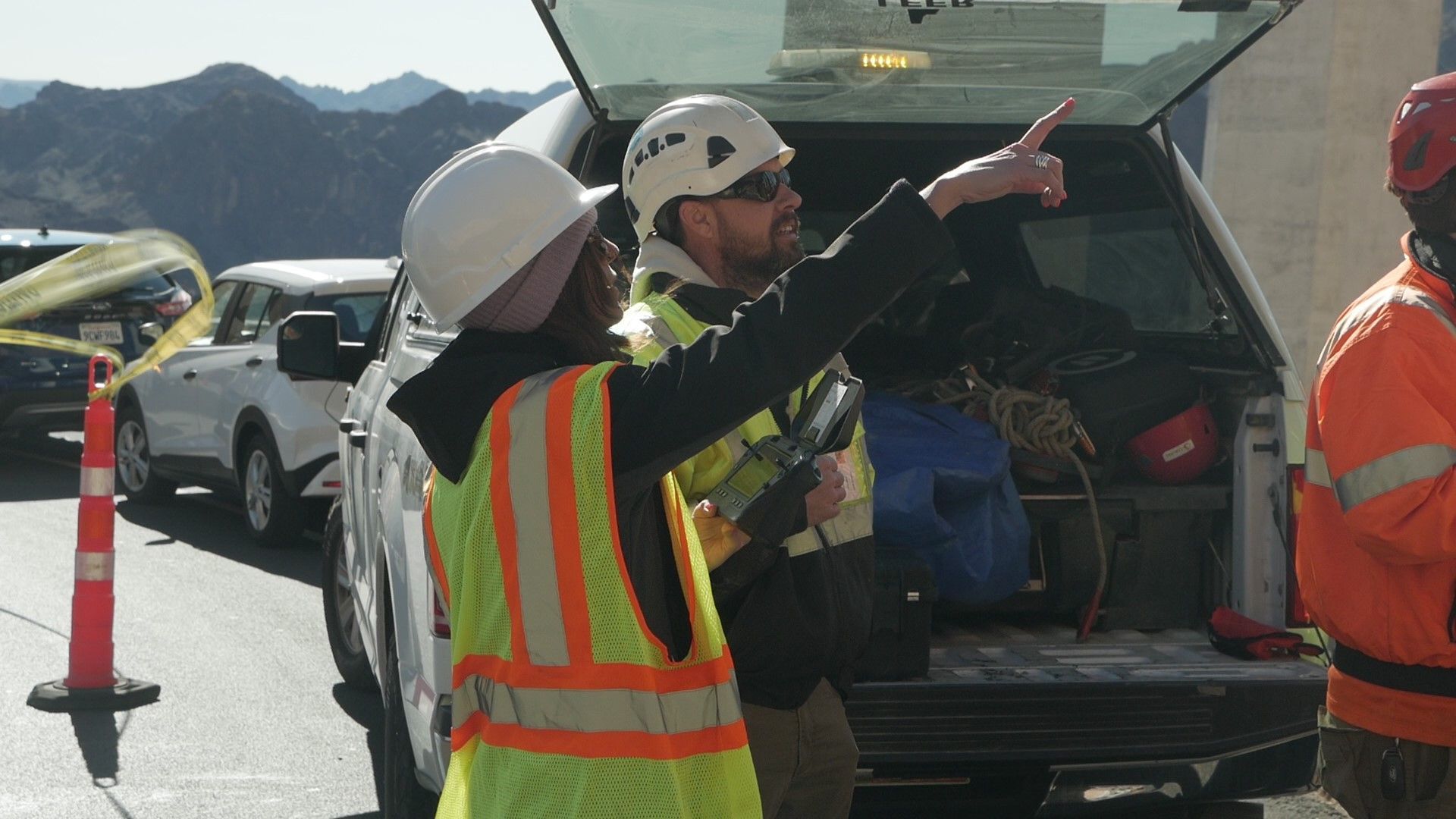
However, while UAS technology is easier to use than ever, you still need to plan up front if you expect to use it effectively, said Josh Sexton, reality capture technology manager and manager of Stantec’s UAS program. In some cases a 2D scan may suffice — and is much faster. “Are you just looking for defects, or do you want to use 3D modeling to map cracks and use machine learning to see how they’re propagating from year to year? You need to have a plan for how you’ll gather data going in and not just figure it out on the back end.”
Professional UAS systems make the data gathering process easier. Skydio’s 3D Scan software automates the workflow. “It allows you to select an asset to scan, and the drone will do all the work necessary to capture every angle of the asset,” said Llorens. “Once the scan is complete, engineers can upload the images to a third-party 3D model generator to create a digital twin.” The data transfers from the drone automatically and resides in the cloud. Skydio offers API integrations to get the data into most photogrammetry systems.
“The software also makes gathering the overlapping images that are necessary to create a 3D model easier,” said Sexton at Stantec. “That’s the beauty of the Skydio system, You set the front and side overlap and it takes care of the rest. And it keeps the ground sample distance (GSD) [the distance between two consecutive pixel centers as measured on the ground] consistent, which helps with the image stitching process immensely.” GSD should be a primary consideration when considering a drone for bridge inspection. Practically speaking, it matters more than simply looking at camera resolution — especially if you are using a drone that can get up close to the bridge components it is inspecting.
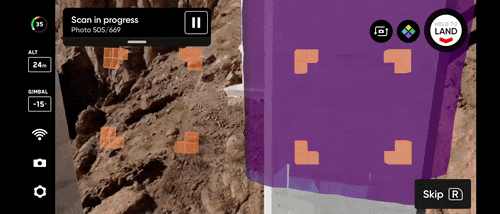
Going forward, real-time visual intelligence is going to be key as we move into a digital revolution, and will be key for following up after catastrophic events,” said Sexton. “In an emergency such as a flood, imagine instead of deploying a team to every asset, employing a UAS solution at every site to see what’s going on in real time on a day-to-day basis.” Indeed, in the wake of Hurricane Ian, Skydio worked with agencies to do exactly that.
How to get started
The cost to get started with a drone inspection program is relatively low, at about $8,000 to $12,000, said Llorens at Skydio. So how do you get started?
- Begin by assembling the right team that includes actual bridge engineers, not just drone enthusiasts.
- Use ROI to calculate your budget, and be sure to review your whole UAS bridge inspection program’s budget, including training and software, not just the equipment cost.
- And when comparing UAS systems, think about your data output, not just the product specs. For example, rather than simply looking for the best camera resolution specifications, focus on GSD and the quality of the dataset you can generate using the UAS system.
Buying traditional drones is less costly, but that’s money down the drain if you need to hire dedicated pilots with outdated workflows — or if the drone crashes and is unusable. “Choosing modern drone systems with the most advanced autonomy and obstacle avoidance technologies is key to scaling the use of UAS for bridge inspection because the systems get the job done faster, can get into hard to reach areas and still navigate when GPS signals drop out, and are easy enough to fly that you don’t need a dedicated pilot at the controls,” said Marshall. “It makes sense for us to have our engineers behind the sticks because they know what they’re looking for,” he said. “I can view the controller screen without worrying about collisions, see exactly what’s going on with the bridge and focus in on details.”
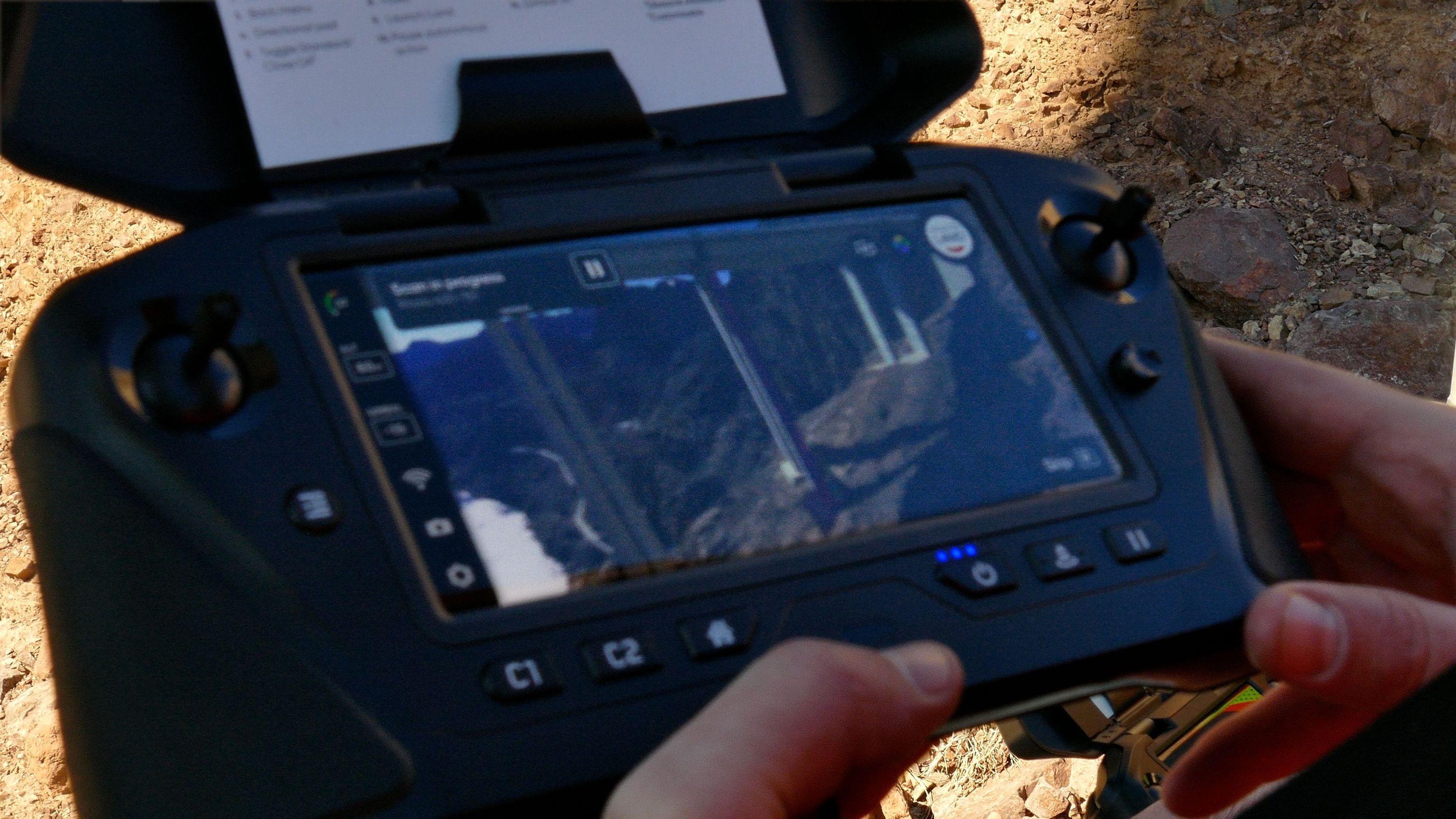
Finally, as you get started, consider that while UAS software optimizes workflows for creating complex 3D models, engineers can begin with simpler 2D scans. For routine surveys, for example, drone teams can make the first pass on a bridge just using the UAS. “A lot of times that’s all you need. You don’t need bucket trucks or hands-on access,” Marshall said. “UAS take a load off your staff, makes their jobs easier and helps you leverage your staff better.”
For more on how Stantec uses UAS in the field, watch the webinar “Optimizing Inspection of the O’Callaghan-Tillman Bridge.”Or check out the full ARTBA Bridge Report.