3D Tower Capture: 3D Scan Gets Smarter With Telecommunication Towers
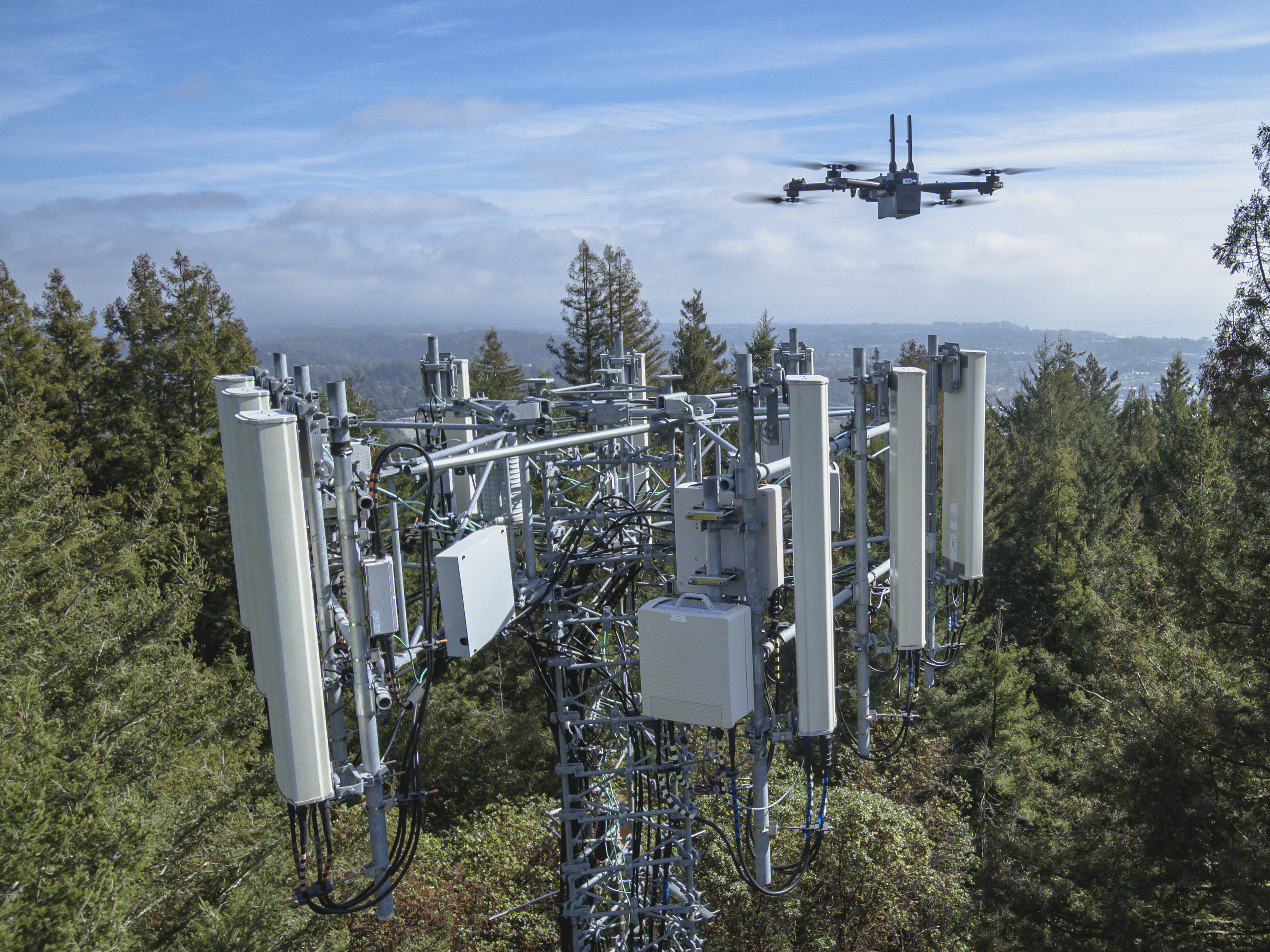
Schedule a demo with our sales team today.
We are excited to announce the upcoming availability of 3D Tower Capture, the latest autonomous capture mode of Skydio 3D Scan optimized for vertical structures, beginning with telecommunications towers.
Telecommunication infrastructure is experiencing explosive growth
The wireless industry has been on an exponential growth trajectory for years as it expands to meet insatiable user demand for more connectivity and data. To put things in perspective, the average cellular data consumption per capita in North America has increased from a mere ~.27GB in 2010 to ~11GB+/ year in 2020, thanks in large part to the development of 5G technology, consumers moving from cable to streaming, and the adoption of unlimited data plans. This immense demand has pushed carriers, tower owners, and turf vendors to their limits. Carriers are on a constant mission to upgrade equipment and add capacity; tower owners are stretched to support build-outs with pre-construction site visits and slow tower loading engineering workflows; and turf vendors are maxing out their personnel trying to support both. Because multiple carriers collocate on a single tower, the industry is forced to manage a constantly changing portfolio of hundreds of thousands of towers annually. Traditionally, these are inspected before and after an installation by a combination of carriers, tower owners or both reading third-party audits.
A ton of work, thrash and rework is created due to a lack of digestible, accurate and actionable data. As a result, multiple organizations often spend tens of millions of dollars annually by having their teams drive hours to inspect the same asset multiple times. Inspecting towers by climbing remains dangerous and expensive, while inspecting assets from the ground is inaccurate, which can lead to rework, missed inventory or network reliability challenges.
Companies must consider many variables when assessing an upgrade or new installation. Line of sight, available space, wind loading, local concealment regulations, access road easements and more. However, even the most basic RAD center analysis can be difficult. Before drones, companies had to choose between dangerous physical tape drops, expensive total station laser measurements or inaccurate digital tape drops with hand held lasers or photos. Today, drones can address many of these challenges by allowing operators to complete inspections, while keeping personnel safely on the ground. Depending on the use case, all have their time and place but for most inspection tasks, I would argue drones have proven themselves to exceed the requirements of the industry both in accuracy and affordability.
So why aren’t 100% of pre- or post-construction inspections conducted with drones
The answer: data capture with manual drones doesn’t scale
In order to get the most out of drone inspections, wireless organizations have adopted photogrammetry, a process of stitching together photos to generate a three-dimensional model. The big benefit of using photogrammetry, in addition to the raw HD photos, is that it allows us to take measurements directly from the digital twin 3D model. Need to see microwave line-of-sight or measure the distance between antennas on a mount? Need to determine a dead-accurate RAD center height or the downtilt of a panel? It’s all possible with photogrammetry.
While the value of photogrammetry is clear, using it at scale directly depends on the consistency and efficiency of the data capture phase. When you have tens of thousands of assets to inspect in a year, the ability to capture a complete and accurate data set as efficiently as possible the first time around is critical to ensure a positive return on investment. The only viable path is through a reliable, automated process that eliminates human errors.
Until now, automated data capture with drones was inefficient and took immense focus and resources to scale. The geometry of towers — thin tall structures — coupled with the complexity of each installation — power and telephone wires, tapered self-support towers, changing elevations of the mission on high-grade slopes, buildings, tree branch encroachment in the compound and, of course, guyed wires — all required expert pilots to spend endless hours programming waypoint missions on a site-by-site basis. It’s simply extremely challenging to scale when you have thousands of towers to inspect.
Enter Skydio 3D Scan: autonomous drone data capture for inspection and mapping
Whether it’s used for towers, bridges or accident scenes, our goal with Skydio 3D Scan is to provide the simplest, most accurate and cost effective way to use drones to capture the photographic data needed to document and digitize infrastructure.
Skydio 3D Scan uses groundbreaking AI to autonomously fly a Skydio drone in and around a structure to capture a complete photoset of every surface necessary to generate highly detailed digital twins, faster and with greater precision than even the most experienced pilot.
3D Tower Capture is optimized for towers
The new 3D Tower Capture mode brings a series of optimizations designed to make scans of vertically shaped structures - starting with telco towers - even faster and more efficient.
Faster and easier setup
The original 3D Capture mode allows users to efficiently scan complex structures by setting a floor, a ceiling and at least three pillars to define a scan volume. While this is a foolproof way of capturing any structure, regardless of shape, towers have simpler symmetrical shapes around their vertical Z axis. This specific characteristic of a whole category of inspection assets, such as towers, means that we can redefine the way the scan volume is outlined. Instead of flying the drone to set multiple pillars, 3D Tower Capture allows you to define the scan volume as a cylinder through four simple parameters. This streamlined process saves battery life and makes the scan setup much simpler and faster:
- Set Floor
- Set Ceiling
- Set Center - a single pillar at the center of the tower
- Set Radius - large enough to enclose the widest part of the tower
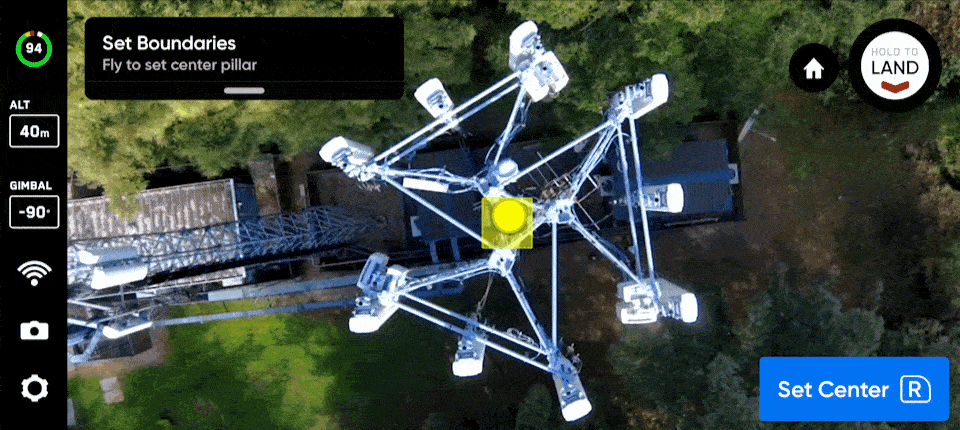
More efficient autonomous capture
One of the most amazing feats of the general 3D Capture mode is its ability to capture images from every angle by having the drone scan across all axes, X, Y, and Z. However, because tower structures are more standardized in shape, a simpler capture flight plan is also warranted. 3D Tower Capture optimizes by defaulting its flight path to begin at the top or bottom of the tower and fly a spiral path around the Z axis. This intelligent planning reduces the number of images that are captured (while simultaneously preserving user-specified resolution settings), which in turn dramatically decreases your total time spent scanning. By starting the scan from the top of the tower, larger multi-battery scans also become more efficient, because the drone has a shorter distance to fly when it repositions itself after the battery swap.
More reliable photogrammetry processing
When processing free-standing structures in photogrammetry software, one common challenge is the large amount of blue sky included in images that are captured horizontally or looking up. Photogrammetry software heavily relies on texture and contrast, so an excess of textureless blue sky makes the final model less accurate. While the general 3D Capture mode can be fantastic for capturing unprecedented detail from the underbelly of assets, in the case of towers, that often exposes the photogrammetry engine to more sky than necessary.
3D Tower Capture defaults the camera gimbal angle to face downward, ensuring your images only contain important textured surfaces. Enable the X and/or Y scan passes and Skydio will intelligently capture horizontal elements, such as the underside of antennas, without capturing excessive or redundant imagery. The sharp look-down angle of 3D Tower Capture will also increase ground capture which will help anchor the model to global coordinates, especially when using ground control points.
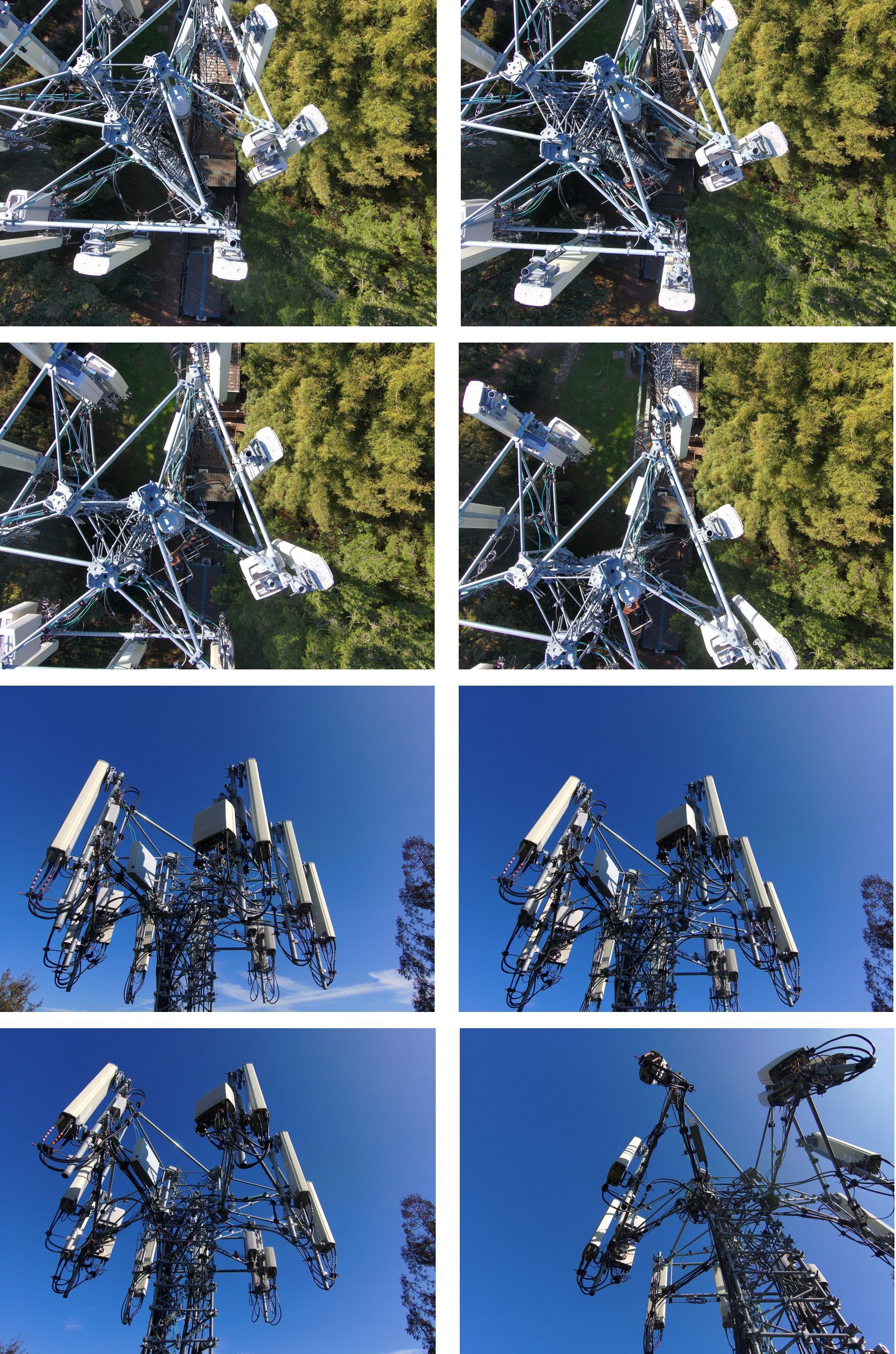
Compatible with leading processing and analysis software
As has always been the case, you can export all 3D Scan photos with full metadata to any third-party photogrammetry software to create 3D models. We actively partner with companies like Bentley, DroneDeploy, Pix4D and RealityCapture to optimize our output for their platforms.
Thanks to our specific enhancements in this realm and technology partners, we are now capable of delivering a complete solution for tower digitization. For example, our partnership with Bentley OpenTower IQ allows you to:
- Capture tower imagery faster and more efficiently
- Create, maintain, and augment your digital twin and compare as-built towers with your asset management system
- Monitor tower health and share data through an easy-to-understand portal
- Quickly turn around designs and design modifications for clients using predictive analysis
In the past eight months, we have successfully proven the value of 3D Scan with customers across industries and use cases. From Sundt Construction using it to safely process a digital twin of a highly complex semiconductor facility for inspection purposes, to Boston PD more efficiently documenting crime and crash scenes to minimize the societal impact, from a defense agency mapping out an entire village to feed their intelligence efforts, to a set of historical assets that can more easily be preserved in digital form.
Responding to the feedback from many POCs, we are constantly enhancing the product to optimize for a wide range use cases. Last October 2021, we delivered 2D GPS Capture, a new 3D Scan capture mode to let users build 2D orthomosaics by planning the flight path using GPS coordinates on a map prior to takeoff. With 3D Tower Capture we are taking the next steps to address the needs of tower inspectors.
If you are one of those professionals and you want to get your hands on a Skydio with 3D Scan, contact our enterprise sales team. For those of you at NATE UNITE 2022, stop by our booth (#130) and meet with our experts.